ロジスティクス入荷が正しく行われれば誤出荷は出ない――ならありがたいのだが、現実はそうならないことが多い。 誤出荷は、いつ、どこで発覚するのか。多くは「着荷」時、つまり配達完了後に検収や開封した際だろう。その内容は「発注したアイテムと違う」「発注した色と違う」「発注した数と違う」などが一般的だ。
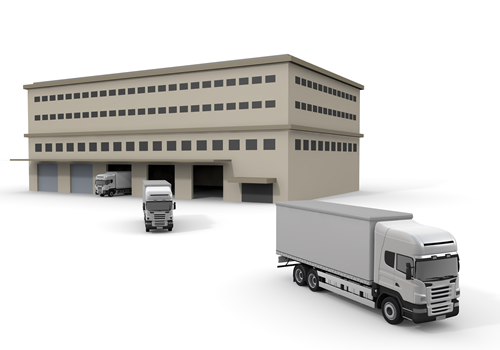
(イメージ画像)
次に多く発覚するのは「庫内」作業時。日次や週次の循環棚卸の際に発覚する。そもそも在庫差異から誤出荷を疑える倉庫は、入荷作業を定石どおりに行っていると推察できる。入荷が間違っていないのだから、在庫が狂う原因のひとつに誤出荷が考えられる。不足している在庫の引当情報をさかのぼって調べ、本来の受注引当品の在庫が過剰になっていれば、誤出荷が原因と確定する。発覚のパターンは異なるにしても、要は誤ピックしているのだろう。全部が全部そうとも断言できないが、ここではあえて言及しない。
■ 機器選定の基準
次にピッカーがどうやってピッキングしたのかに焦点が定まる。OJTどおりの手順を違えていないかのヒアリングなどがロールプレイで確認される。その次は、誤ピック品がなぜ梱包されてしまったのかに移り、最後は納品データとの照合作業にまで及んで、送状貼付作業の確認で検証は完了する。
裏を返せば、上述したいずれかのフェーズで事件は起こる。筆者の感覚では、それが不可抗力だったことは皆無に近い。おおむね人災であり、魔が差したかのような「わかっていたんですが、つい」といった類の言葉で表現される中身である。
不意の惰性や怠慢を抑止する最良の術は、業務フローの研磨とOJTの徹底なのだが、現場責任者や物流管理者の能力によって成果が変動するところまでは制御できない。もっとも、そこまで検証や議論を突き詰めたうえで利器を導入するのであれば大いに効果が期待できる。依存ではなく補完として道具を採用するなら、技術の一部として有効だろう。 では、道具選定の基準として何を主眼に置くべきなのか。
第二に「明瞭」であること
第三に「視覚聴覚に訴える」こと
■ 優れた利器の共通点
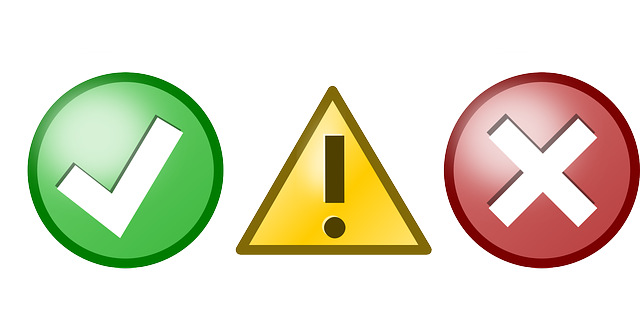
(イメージ画像)
誤ピックや梱包ラインでの最終チェックにしても、道具の形態種別にかかわらず、音声や画面上で視聴覚に訴える機能が最も効果を生み出す。音も画像もマルバツを区分する効果音や記号の表示で十分。エラーの種別や内容に関する冗長な説明や、警告後に何らかの操作をして次の画面に遷移して読んだり見たりしなければならないような仕組みは、現場にとってありがたくないモノの典型だ。
現場ではどの作業分野であっても、エラーが認知できればすぐにその因を探って修正や報告ができる。なぜなら作業者は端末で説明されるまでもなく、エラーの種別を熟知しているからだ。したがって、補助具たる各種機器やシステムの第一目的は「注意喚起」もしくは「警告」であり、指導や修正補助ではない。「まちがっている」ことを報せてくれれば十分である。
それゆえに凝った作り込みは不要。ひたすらに操作簡易で明瞭極まりない表示や発音といった機能を持つ利器は、高機能を突き詰めて単純化しているのであって、決して安直でも安易な設計製造技術でもないことを付記しておく。必要な要素を全部載せたうえで、あたかも「木材をノミで削り、きれいな彫像を生み出す」に等しい作業の成果物であるということが、優れた利器の共通点だ。誤出荷を無くす道程の携行品を選ぶ際には、是非心がけてほしいと思う。(企画編集委員・永田利紀)