話題物流の現場では、ベンダーやマテハンメーカーが協力して物流現場のDX(デジタルトランスフォーメーション)化を企図する取り組みが広がっている。23日、そんなメーカー同士の協調・協働の実態を紹介するイベント「第二回物流DX会議」が開催された。
昨年行われた第1回では、各社が連携の必要性を新たにした。その成果を確認するべく開催された第2回には昨年の3倍にあたる18社が参加、8つの取り組みが紹介された。ここでは3つの連携事例を取り上げる。
APT × ストラソル
マテハンメーカーが乱立する昨今、そのなかから自社に合った機器を発掘することは容易ではない。またメーカーの選定から契約、機器の導入に至るまで、DX化に際して現場にかかる負荷は膨大だ。APT(アプト)とストラソルアーキテクトは、メーカーレスな提案を行うことで、そういった荷主企業・運送事業者の業務負担軽減を目指す。
今回、APTからはソリューション営業本部部長の栗原勇人氏が、ストラソルアーキテクトからは社長の秋川健次郎氏が登壇した。
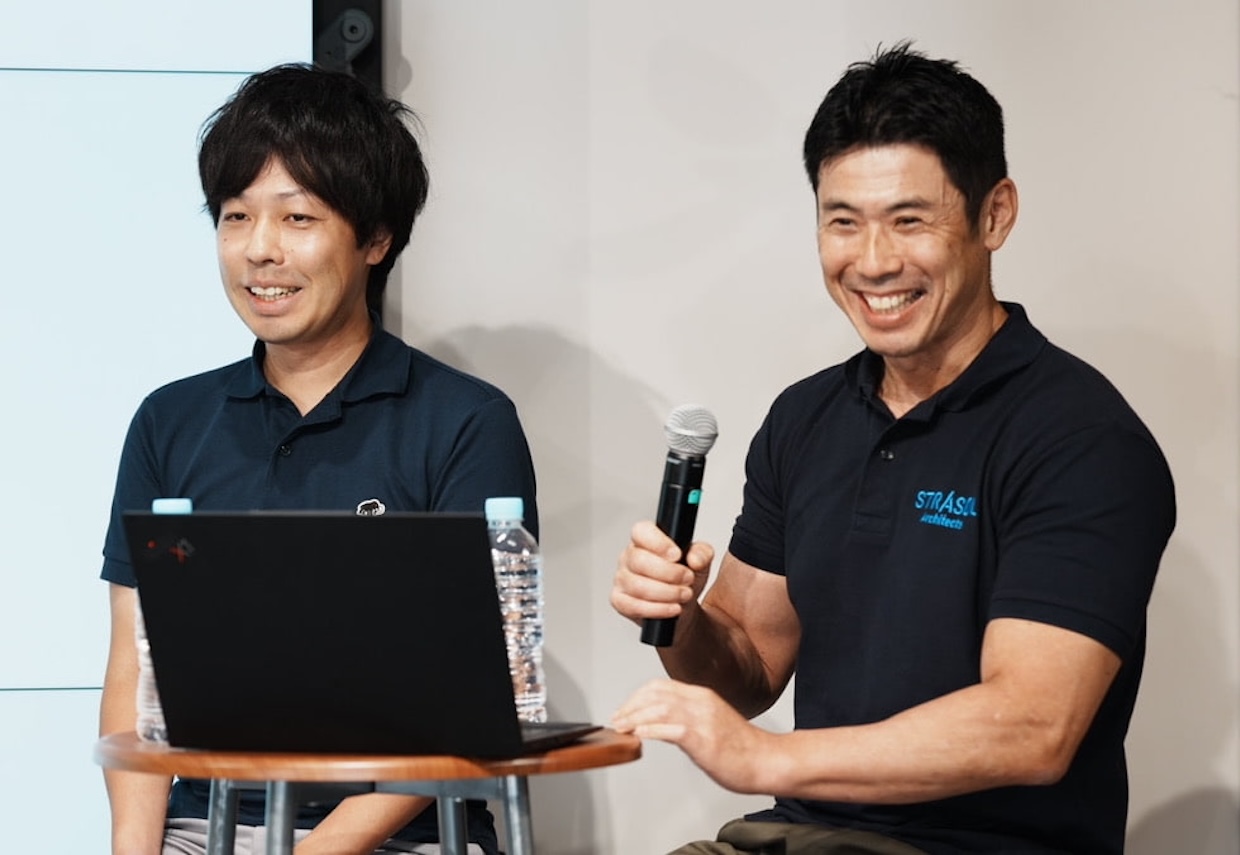
▲(左から)APTの栗原勇人氏、ストラソルアーキテクトの秋川健次郎氏
秋川氏は「物流は人と機械、それを包括する仕組みの3つで成り立つもの」と前置きした上で「人件費は高騰し、機械の値段も上がっている。物流コストを抑えるには計画性を持って仕組みを整える必要がある」と語る。
ともにシーアールイーグループに属する両社は「TUNAGERU(つなげる)インテグレーション」というコンセプトのもと、物流の仕組みづくりに取り組んでいる。両社には明確な役割分担があり、ストラソルアーキテクトはユーザー向けに物流施設運用の企画・構想を練り、その実行手段を具体的な形にしていくのがAPTだ。
その際には現場にとっての最適解を導き出すため、メーカーレスな提案を心がけるという。「マテハンメーカー主体だと、どうしても自社製品を最大限生かすような提案が主体になる。また、製品が現場にうまく合わない場合であっても、代替案を出されにくい」と秋川氏。続いて栗原氏が「メーカーの選定、契約、発注など、仕組みを整えるまでには大変な労力がかかる。われわれはそこを肩代わりすることでDX化を推進していく」と話した。
APTの強みはこういった提案力にとどまらず、異なるメーカーのシステムを連携させられる点にある。提案ベースで終わることなく、倉庫がしっかり稼働するまで仕組みを煮詰める。物流コスト最適化のためなら、マテハン機器の導入にもこだわらない。実際、とある事例では自動倉庫を撤去し、従来の人を主体にした倉庫に戻した。
さらに両社は新サービス「Logiドック」を展開。物流改革をしたくても何から着手していいか分からない企業向けに、企業の物流を戦略、ルール・組織、業務、システムという4つの視点から診断、改善の道筋を示すというものだ。ここでもストラソルアーキテクトの提案力とAPTの技術力が生かされる。
DX化を企図していても、選択肢が多すぎるゆえに途方にくれてしまう企業も多い。APTとストラソルアーキテクトは迷える物流事業者のコスト最適化をはかり、その仕組みづくりを強力にサポートする。
ギークプラス × ロジザード
庫内向けの搬送ロボットを開発するギークプラスと、クラウド型WMS(倉庫管理システム)を提供するロジザードは、アパレル現場での協働の実態を紹介した。
登壇したのはギークプラス営業部本部長で執行役員の嶋田由香里氏と、ロジザード営業部執行役員・部長の柿野充洋氏。
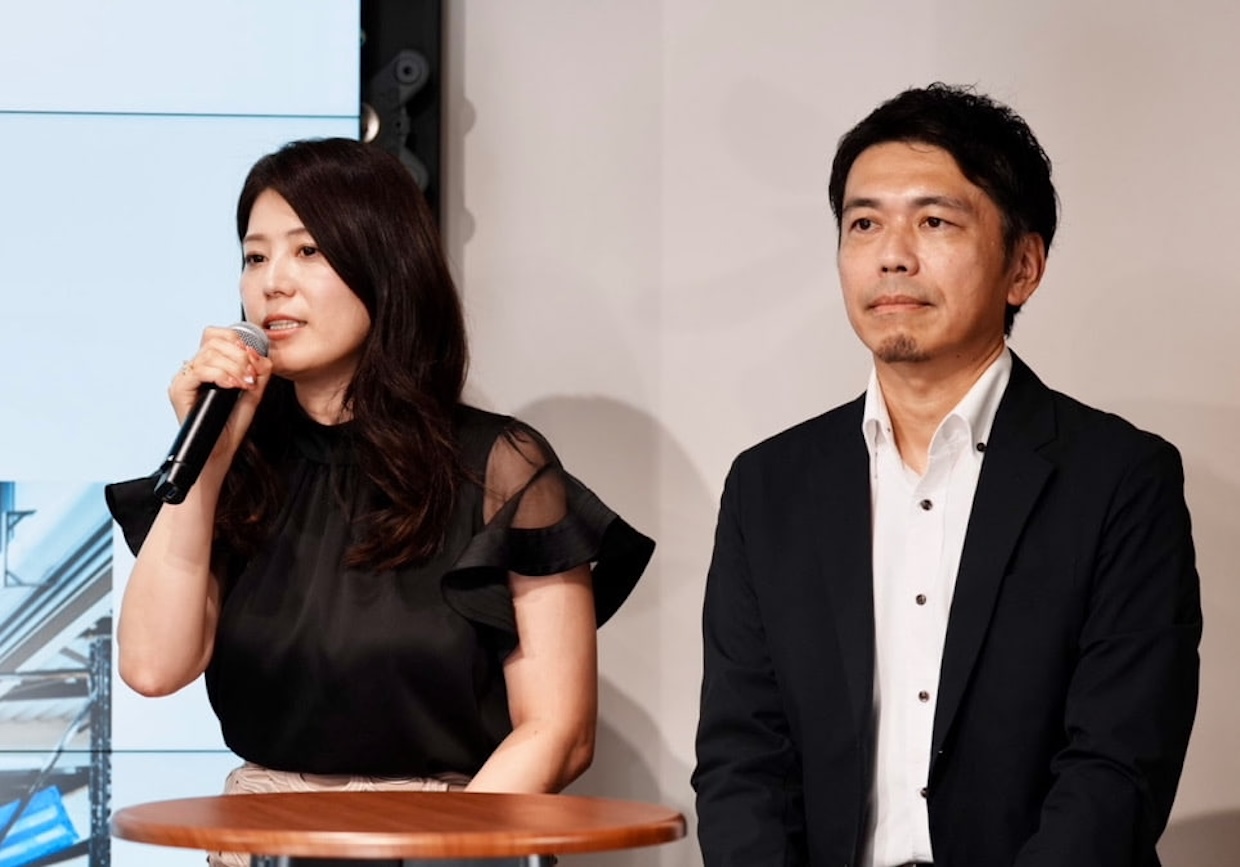
▲(左から)ギークプラスの嶋田由香里氏、ロジザードの柿野充洋氏
今回、協働の現場として具体的に名前が挙がったのはアパレル会社のジェイ・ビー(大阪市北区)。近年、大手荷主企業などによる大型物流施設の建設が進み、集積地域では労働力の奪い合いが起きている。規模で勝る大手荷主企業の進出を受け、自社で物流を担うジェイ・ビーは慢性的な人手不足に陥った。
導入コストの関係で、中小企業は大手荷主企業のように大規模な設備投資をすることが難しい。また、アパレル商品はSKU(商品の最小単位)が非常に細かく設定されているため、デザインが同じでもサイズや色が違えば、異なる商品としてカウントされる。ましてやジェイ・ビーは全国60か所以上の店舗に商品を発送しており、仕分け・発送のフローは複雑だ。
コストと荷姿との兼ね合いで、両社は倉庫の半自動化を目指すこととして落ち着いた。そこでギークプラスは搬送ロボットを、ロジザードはDAS(仕分けシステム)提供。その結果、一方でギークプラスのロボットが段ボールを運び、もう一方では作業員がDASシステムを利用して商品を仕分けるといったシステムが構築された。
2社は導入後の現場の様子を動画で紹介。庫内作業員のインタビューでは、システム導入によって生じたメリットについて「以前は台車を引いて倉庫内を歩き回っていた。半自動化のおかげで今は棚入れの時間は半分以下に抑えられている」と話した。
こうした結果を受け、ジェイ・ビーはロボットの追加導入も検討している。ジェイ・ビーの経営陣から話を受けた際、ギークプラスの嶋田氏はその場で導入コストや作業効率の伸び率について具体的な数字を挙げることができたという。「DXの強みはデータで語れること。ユーザーの要望に具体的な数字で応えることができる」(嶋田氏)
ロジザードの柿野氏は「われわれはシステムを複雑にしないためにもカスタマイズはなるべくしない」としつつ、「それでもほかのシステムと連携するために変えるべきところは変える。協働化のメリットはそれだけ大きい」と話した。
セーフィー × アイオイ・システム
連携事例の最後に登場したのは監視カメラで現場を可視化するセーフィーと、DASシステムを提供するアイオイ・システム。2社が協働して開発したソリューションを利用するクライアント企業を交えての登壇だ。
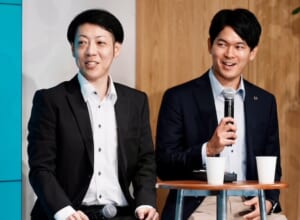
▲(左から)アイオイ・システムの江田雄輝氏、富士エコーの岡篤司氏
セーフィーからは営業部物流ソリューショングループ、サブグループリーダーの派谷翔太氏が、アイオイ・システムからは江田雄輝氏が登壇。さらにゲストとして、フジパングループの子会社である富士エコー(千葉県市川市)営業企画課係長の岡篤司氏を迎えてディスカッションが進められた。
富士エコーは全国16か所にパンなどの食品保存用の倉庫を持つ。同社では納品後の過不足が生じた際の原因把握に手間と時間がかかっていた。発送先で商品の数が合わないと、確認のために倉庫に連絡がいき、それを受けて担当者が原因の把握に乗り出す。作業日のログを抽出した後、監視カメラの映像を巻き戻して地道にチェックするという方法が取られていた。この作業には平均して10分ほどの時間がかかっていたという。
しかし、アイオイ・システムの「仕分けの達人」とセーフィーのクラウドカメラを組み合わせることで確認時間の大幅な短縮に成功した。
まず、「仕分けの達人」を導入し、ピッキング作業の効率化を図った。このソリューションではまず、その日のピッキング作業をデータとして入力。バーコードを読み込むと、ラックに設置されたカラフルなLEDライトが点灯し、自分の担当する色が点灯しているラックから指定された数だけ商品をピックするだけだ。リストによるピッキングよりも直感的なためミスが生じにくく、しかも作業時間の大幅な短縮が期待できる。
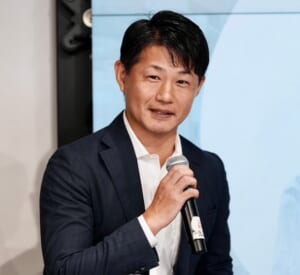
▲セーフィーの派谷翔太氏
セーフィーのクラウドカメラは、万一ピックミスが起きてしまった場合に備えてのものだ。仕分けシステムによって店舗コードと商品コードが映像に紐づけられているため、作業者は2つのコードを入力するだけで、すぐにピックミスが起きた際の映像を振り返ることが可能だ。また、セーフィーのカメラはクラウド型のため、通信環境さえあればどこでも確認できる。富士エコーはこれにより、平均10分かかっていた確認作業が30秒ほどにまで短縮されたという。
富士エコーの岡氏はユーザーの立場から「富士エコーは事故ゼロ、クレームゼロを目指している。2つのソリューションを導入したおかげで目標達成に一歩近づいた」と話した。