話題1963年に創業し、日本で普及していなかったアルミ製トラックボディーを日本で初めて量産化した輸送用機器メーカーの日本フルハーフ(神奈川県厚木市)。国内カーゴ系架装4大メーカーの一社に数えられ、現在、全国7か所の直営工場と200か所以上の指定サービス工場を展開している。高い輸送効率や燃費性能、環境対応と時代とともに市場ニーズは変化し続けるが、半世紀以上にわたって一貫しているのは「顧客に寄り添ったものづくり」。物流事業者がドライバーの働き方改革や脱炭素化、車両の電動化に向けた動きを本格化させるなか、激変する業界の現在地をどのように捉え、今後の製品開発に取り組もうとしているのか。日本フルハーフの田中俊和社長に話を聞いた。(編集部・安本渉)
──2022年の振り返りとともに、足元の事業の進ちょく状況は。
自動車のシャシメーカーの半導体不足や中国・上海のロックダウン(都市封鎖)が響き、トラック生産が2、3年前に比べて3分の2程度にまで落ち込んでいる影響が大きい。トラックのシャシがなければ、架装の仕事は始められない。納期が1年以上伸びてしまうケースも出ている。新型コロナウイルス禍を契機に、巣ごもり消費が伸びて冷凍食品の市場が拡大し、温度管理車の受注は2021年上期までは健闘していたが、その需要は一巡したという印象。アルミをはじめ世界的に原材料費が高止まりしており、会社全体としては厳しい事業環境が続いている。
──今秋に8年ぶりに投入した「大型トラック用ウイングボディー」には、ドライバーの働き方改革や環境対応などを意識した開発コンセプトが随所に見られる。
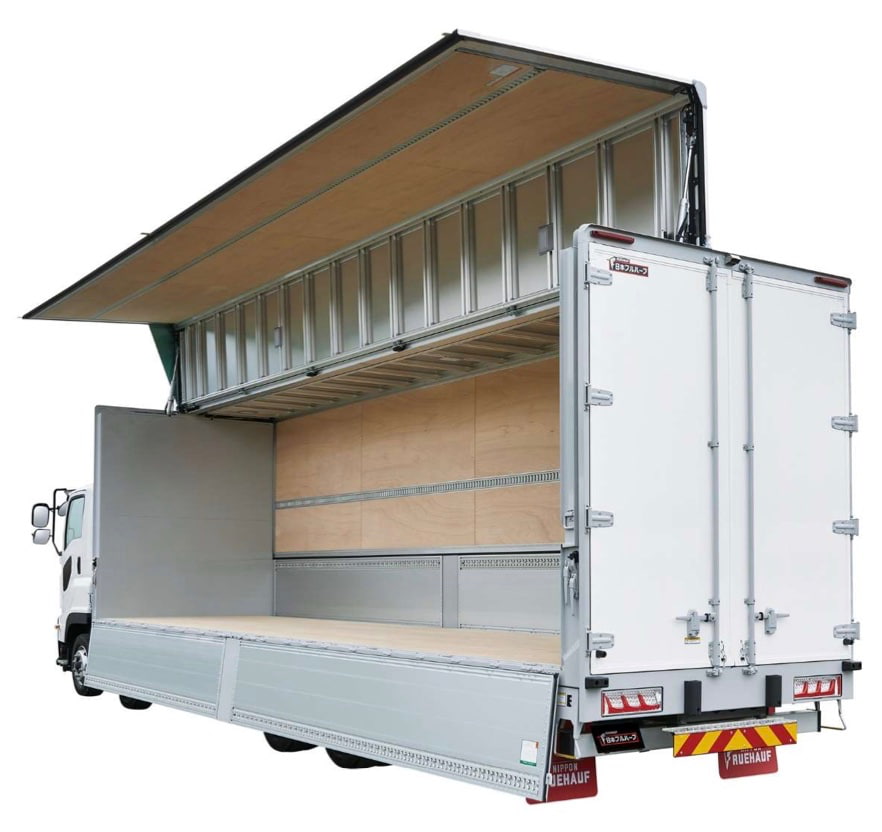
▲大型トラック用ウイングボディー(出所:日本フルハーフ)
24年4月から、ドライバーの労働時間に上限規制が設けられる「物流の2024年問題」が迫り、架装メーカーの事業にどのような影響が出るのか注視しているが、それに伴うユーザーニーズの変化を見通すことは難しい。気候変動やCO2排出量を削減する脱炭素化も避けては通れない課題だ。本当の意味でのモーダルシフトがこれから本格化していくなかで、トラックは単位重量当たりのCO2排出量で船舶や鉄道には敵わない。しかし、船ですべてのモノを運ぶ時代になるわけではない。近年多発する豪雨などの自然災害で、鉄道の脆弱さも露呈している。小回りが効くトラックの利便性は今後も変わらないだろう。
──自動車産業は「100年に一度」の変革期を迎える中、いわゆる「CASE」への対応は。
トラックをはじめとした大型車両に関しては、急激な電動化への対応の方向性にも注目している。電気だけでなく、水素や別の動力が主流になるという見方もあり、社会や経済の動向を踏まえた車両に合った最適な架装を開発していかなければならない。例えば、EV(電気自動車)トラックは電池の収容スペースが大きくなる可能性がある。その場合、荷台に搭載するという設計が一般的になることもあり得る。そうなると、いかに荷台の中のスペースを有効活用するかの工夫が必要になってくる。これまで以上に完成車メーカーとの連携を密にしながら製品開発を進めなければならない。
──具体的には、将来架装メーカーにはどのような対応が求められるのか。
例えば、温度管理車は現在、エンジンからの十分な動力供給で庫内を冷やしている。しかし、将来的にEVが普及すると、いかに限られた動力を活用して庫内の温度管理を効率的に行うかがポイントになってくる。空気の流れをセンサーで検知して、電力消費を減らすといった機能が求められるだろう。また、ガソリン車とEV車、水素エンジン車と動力が異なる車種があった場合、その特性に応じた架装が必要になり、現状のままでは生産する車種・車型が倍増する可能性がある。そうなると基本設計の見直しや部品の共通化などを大きく見直す必要もでてくる。さらに、もし将来的にトラックの完全自動運転化が浸透して車の衝突事故がほぼ起きないという時代になれば、現在ほどのボディーの強度は求められなくなり、環境面を考慮した部材の一部変更なども十分起こりうる話だ。
──ボディーの最適化は輸送品質や業務の省力化・効率化にも直結する。開発技術力をどのように強化していくのか。
顧客ニーズに基づき、求められる機能を具現化していくという基本姿勢はこれからも変わらない。一方で、環境問題でいえばCO2排出量が少ない材料で開発・製造を行っていかなければならない。架装メーカーからユーザーへの積極的な提案が一層求められる。
──顧客に寄り添ったものづくりを継続するため、どのように物流業界と向き合っていくのか。
弊社は中国とタイに関連会社がある。これまでは日本から海外へ製品を持って行って改良や開発を行うことが多かったが、今後は法的なハードルが日本よりも低い海外で実証・商品化した後に、日本に「逆輸入」する事例が増えてくるかもしれない。時代や市場の環境が変化しても、大切なのは「ものづくりの力」を高め続けていくこと。そのために不可欠なのは国内外を問わない幅広いユーザーとの日頃からのコミュニケーション。そこから開発ニーズを発掘して吸い上げていきたい。