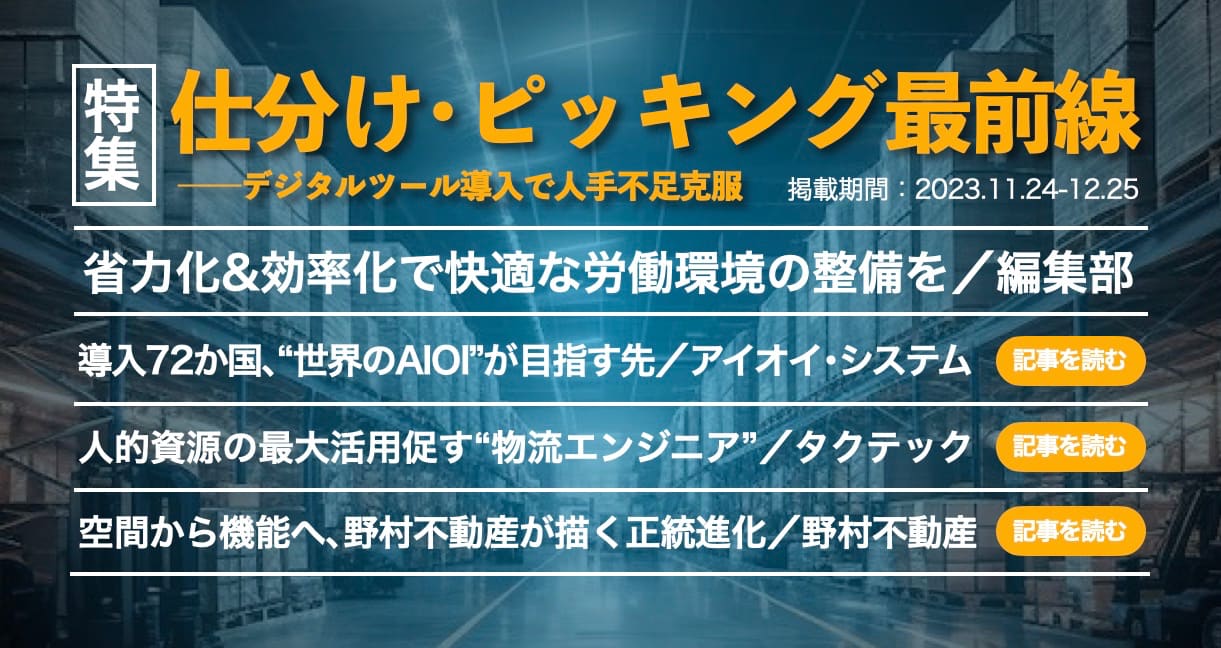
話題物流の仕分け・ピッキング現場における人材不足は深刻だ。EC(電子商取引)需要の拡大は、取り扱い商品の多品種少量化による仕分け・ピッキング作業も煩雑化させ、作業従事者が足りない状況の慢性化を招き、解決策としての省人化・自動化を目的としたソリューションの導入にも注目が集まる。
人材が定着しない仕分け・ピッキング現場で必要となるIT
スキマバイトサービスのタイミーの調査では、スキマバイトにおいて「よく選ぶ仕事」(複数選択可)として物流倉庫内の「仕分け・検品」が全体の52.3%で1位、「ピッキング・梱包」が46.3%で2位、「荷上げ・荷下ろし」24.6%で4位となるなど、物流現場は働く側にとって都合の良い時に受け皿がある仕事と認識され、一方、雇用する側にとっては、こうした臨時アルバイトなど、多様で流動的な雇用形態で現場が支えられている現状が浮き彫りになる。仕分け・ピッキング現場への「定着」を希望する労働者の少なさが、サプライチェーン全体に悪影響を及ぼすことも想定される事態である。
こうした現状から、仕分け・ピッキング現場は年齢・性別・国籍を問わず「誰でもできる」ことがオペレーションの必要条件となり、指導やスキルを必要としないシステム作りが必要とされることになる。物流業界全体の3Kイメージや、単純作業となりがちな業務特性、賃金と労働時間のバランスなどから考えても、今後もさらに「作業者の取り替え」を前提としたオペレーションの構築、省人化を進めなくてはならず、デジタル化、自動化システムを導入する・しないではなく、どんなシステムを運用するかを検討している事業者も多い。
富士電機による2020年のアンケート調査「製造業におけるピッキング作業のデジタル化とデジタル機器の利用動向調査」では、デジタルピッキングシステム(DPS)を「すでに利用している」割合は66%。「今後、利用を検討している」も25%としている。同じくデジタルアソートシステム(DAS)では、「すでに利用している」60%、「今後、利用を検討している」29%と、こちらも活用に肯定的であり、商品管理や検品工程からの延長としてのハンディーターミナルやバーコード活用は、かなり浸透していることがうかがえる。DPS・DAS導入検討のきっかけとして「業務効率、生産性の向上のため」が47.5%、「ミスやクレーム削減のため」44.5%、「人手不足、省人化のため」40%が上位を占めており、今後ますます労働人口の不足が深刻化することや作業のスピードアップが求められることで、さらにシステム導入が後押しされ、機能強化に向けた取り組みにも拍車がかかると想像できる。
「摘み取り式」「種まき式」の基礎知識からピッキング運用を再考する
自社運用に適した、さらに一歩進んだピッキングシステム導入においては、現場の実情と合わないオペレーションが、非効率となる要因となっているケースもあり、改めて現在の運用状況を見直しておくことがすべての出発点である。まずは基本的なことではあるが、「摘み取り方式」(シングルピッキング/オーダーピッキング)と「種まき方式」(トータルピッキング)に大別されるピッキング方式の、どちらが自社の運用に合うかを理解することが、新しいシステム導入においての基盤となる。
「摘み取り方式」では、1つの出荷先のオーダーに対応して庫内の製品を集める方法。ECなど、たくさんの出荷先に多品種の商品を発送し、一出荷あたりの出荷量があまり多くない業種に適している。メリットは1件ずつの対応でミスが少ないこと、梱包から出荷までの工程をスムーズに完結できること。デメリットは作業者が庫内を何度も往復することで歩行距離が長くなり、労働負荷が高くなることにある。
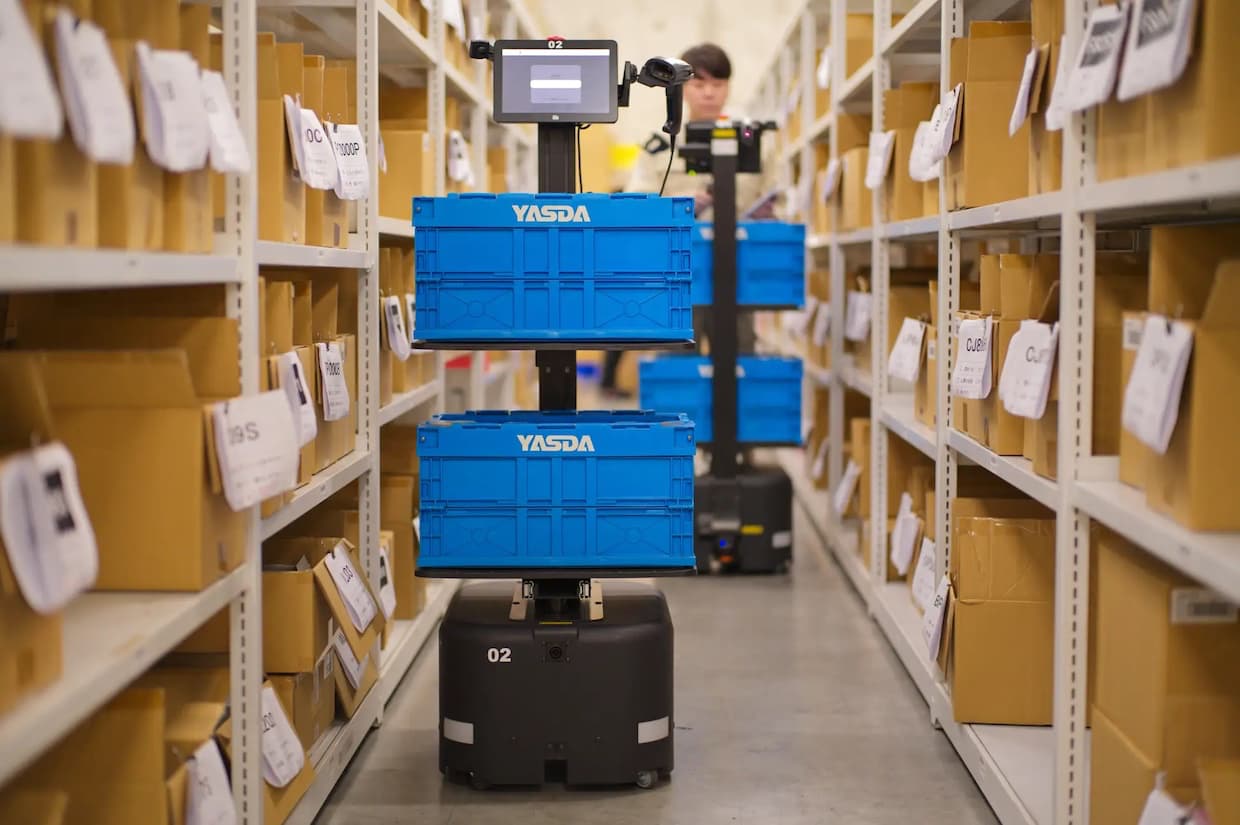
▲作業員と協働するラピュタロボティクス製のAMR(出所:安田倉庫)
「種まき方式」では、複数の出荷先のオーダーとそれに必要な製品もまとめて集めてから、後で出荷先ごとに仕分けする方法。出荷先、商品の種類ともにあまり多くないが、一出荷あたりの出荷量が多いtoB向けの業種に適している。メリットは、まとめてピッキングするため庫内の歩行距離が短くなること。デメリットはピッキングと仕分けの2工程となり、仕分け用のスペースが必要となることや、オーダーをまとめる過程の非効率、ミスが多くなる可能性が挙げられる。
どちらの方式を選択するかは、「取り扱いアイテム数」「出荷先数」「注文数」の分析を指針とし、庫内スペースと稼働状況と合わせて見直すべき最初のステップとなる。また、庫内のロケーション管理との整合性とも関連しており、「固定ロケーション」「フリーロケーション」に大別される庫内のロケーション設定について、現状の運用で課題がないのかも合わせて検討することも必要だろう。
ピッキング効率向上のための、ロケーション他管理システムの再考
ロケーション管理における「固定ロケーション」では、アイテムごとに場所を決めて保管する。シンプルな保管方法のため、欠品管理が容易でありピッキング効率も高く、取り扱いアイテムが限定されている業種に適している。デメリットとしては空きスペースができても別アイテムを置くことができず保管効率が悪くなること。最初の棚割り次第で作業効率が大きく変わり、新アイテム追加ごとの変更にも労力を要することが挙げられる。製造業や病院などtoC領域で、在庫を切らさないことが重視される業界で導入されている。
一方「フリーロケーション」は、空いているスペースに随時入庫する方法。保管効率が高く、商品入れ替えがスムーズで、棚割りの必要もない。ただ、最大限に効果を発揮するためには、在庫管理システムやWMS(倉庫管理システム)との連携が必須であり、運用自体を再構築する発想となるだろう。また、作業員にとっては保管場所の共有が困難なことからピッキング作業効率の低下を招く恐れがあり、ピッキング時の移動距離が長く非効率になってしまう可能性もある。入れ替えの頻度が高いアイテムや、在庫量の変動が多い商品、ロット管理が必要なアイテムの管理に適しているとされ、ネット通販、アパレルなどの業種で活用されている。
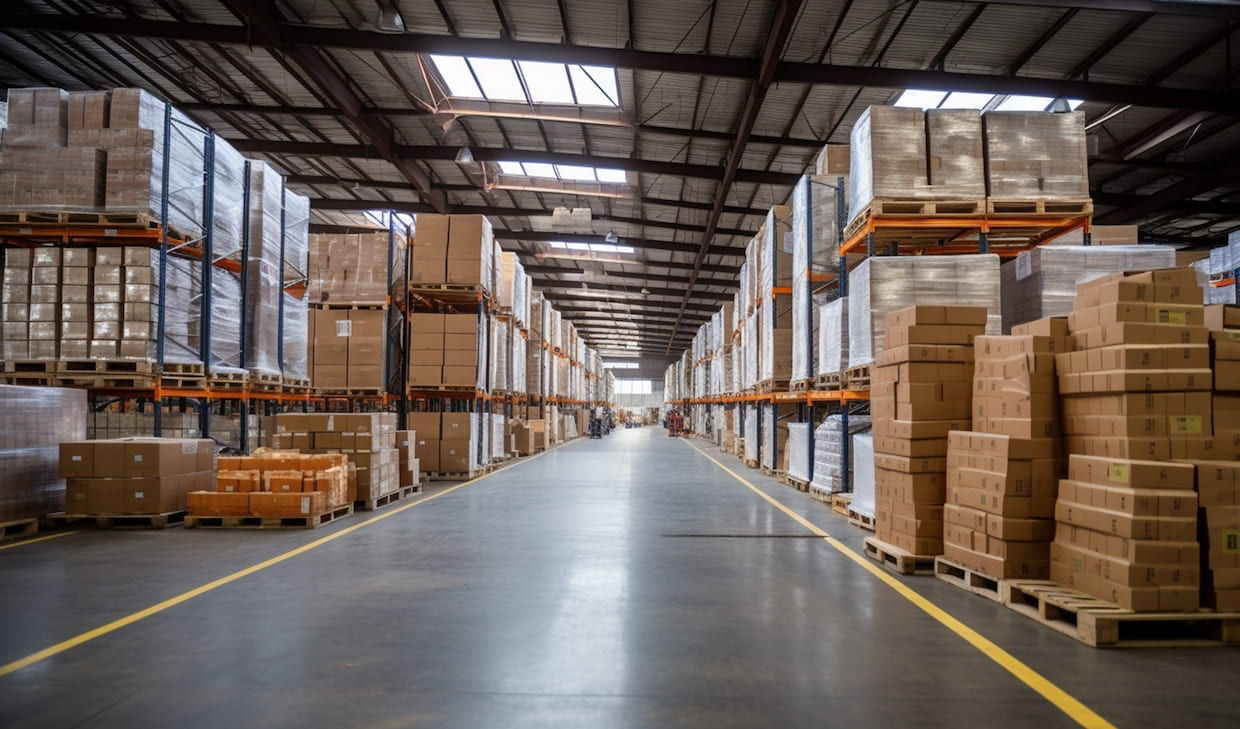
(イメージ)
その他、スペースに余裕があれば、ピッキングエリアは固定、ストックエリアはフリーとして併用する「ダブルトランザクション」という方式で、ピッキング効率と保管効率を両立させるなどの運用もあり、それぞれの長所・短所、商品適正を把握することから最適な運用を選択できる。
そもそも、課題を抱えた庫内現場においては、棚番号の振り分け方や、エリアの色分けだけでも運用効率は大きく変わることもあり、データ分析を伴う抜本的な運用変更には、専門的なコンサルティングも外せない。さらに庫内管理システム導入を伴う変更となれば、最適化の道筋や選択肢も変化するかも知れない。まずは現場の課題をしっかりと把握し、どこを改善するか、マイナーチェンジか、より大がかりな改変かなど、目標を見定めて「検証する」作業自体が重要である。
さまざまなデジタル機器から、ピッキング・仕分けツールをどう選ぶか
最適化への道のりは、各現場ごとにさまざまであり、現場の特性と課題を把握したロケーション設定、ピッキング方式が明確になれば、そこに導入すべき具体的なデジタル機器のイメージもより明確になるだろう。「デジタル表示器」「音声ピッキング」「スマートフォン式」「タブレット式」など、さまざまな種類のデジタルピッキングシステムそれぞれの特性を把握することが大切である。
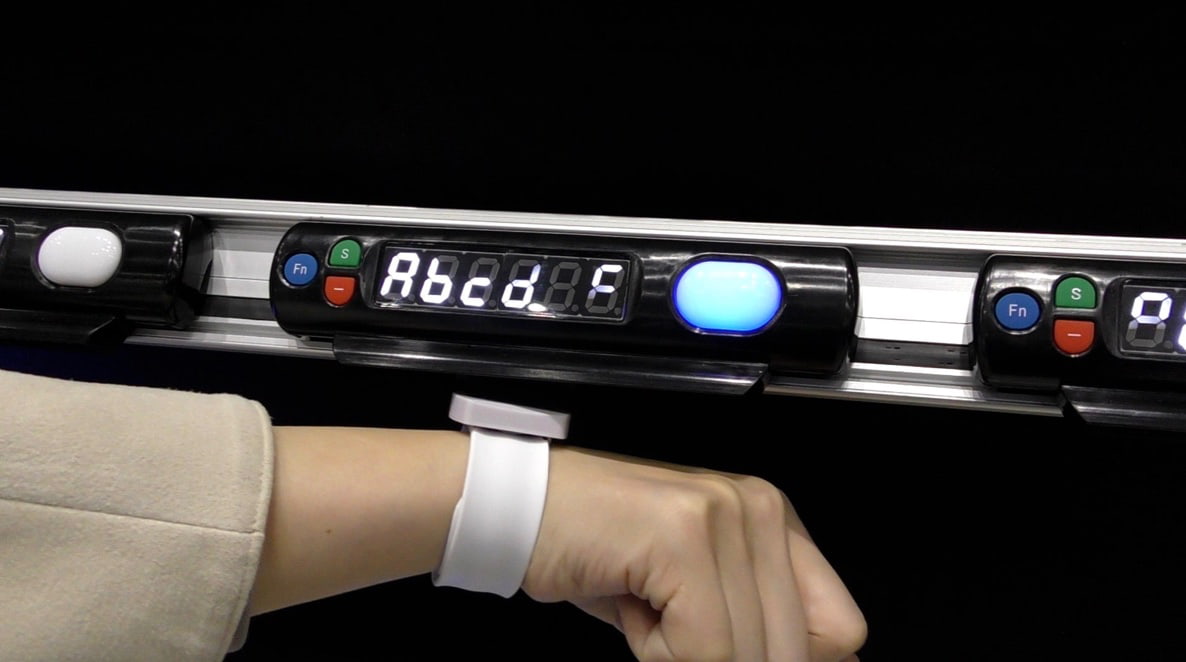
▲アイオイ・システムのRFIDリーダー搭載デジタルピッキング表示器(出所:アイオイ・システム)
「デジタル表示器」によるデジタルピッキングは、誰にでもわかりやすく作業を平準化し、作業効率の速さにおいても優位性があるが、庫内全体をシステムに組み込む導入費用やロケーション設定との整合性などは確認が必要だ。作業速度ではデジタル表示器に劣るが、ハンズフリー・アイズフリーでのフォークリフト作業との併用や、丁寧な取り扱いを必要とするアイテムでは「音声ピッキング」も選択肢となろう。普段使い慣れている携帯などからの移行がスムーズで、作業員にとって使い勝手が良く安価な「スマートフォン式」もある。アイテム分類が細かすぎるために棚ごとに表示器をつけることが非効率であれば「タブレット式」でロケーション確認するのはどうか。台車と組み合わせればピッキングと仕分けを1工程でまとめて行うマルチピッキングカートとして利便性を上げる運用ができる。表示器や読み取り札などを取り付けられない棚・ラックには、「プロジェクションマッピング式」の導入も考えられる。また、出荷頻度の違いによって、固定ロケーションごとに複数のシステムを併用するといったプランもあり得る。
いずれの導入でも、まずは「ペーパーレス化」による作業効率向上において前進となるのは間違いない。さらにデジタル化で期待される「仕分け、ピッキングミスの防止」「人件費削減」「作業の平準化」「実績・データ管理の精度向上」では、各システムの特性ごとに多少の優劣がある。どの項目での改善を重視するか、費用対効果との兼ね合いの中で判断する必要があるだろう。
効率化成功のカギは「ひと」との共存と「庫内見える化」
前段で紹介したデジタル表示器、ハンディーターミナルなどのシステムは、既存のオペレーションからの移行がスムーズであり、「業務効率、生産性の向上」「ミスやクレーム削減」を最優先としたものである。仕分け・ピッキング作業者の生産性を向上させ、人為ミスを防ぐ対策のスタートとして合理的と言えるが、さらにその一歩先、先進的でスケールの大きなオペレーションや「自動化倉庫」とされる作業現場では、仕分け・ピッキング作業者の非効率な「歩行」を排除したソリューションも多数登場しており、省人化技術も加速しているのがわかる。
現状もっとも先進的な仕分け・ピッキング現場の自動化・省人化ソリューションとされているのは、保管ラック自体をAGVでピッキング作業者のもとに移動させるGTP(goods to person)システムや、オートストアなど保管型自動倉庫からロボットが自動ピッキングして作業者のもとに運ぶシステムなどになろう。庫内全体を再構築し、効率化、ミスの削減などを高いレベルでクリアするとともに、作業員が「歩行」する作業さえ無くして高度な効率化が実現できる。
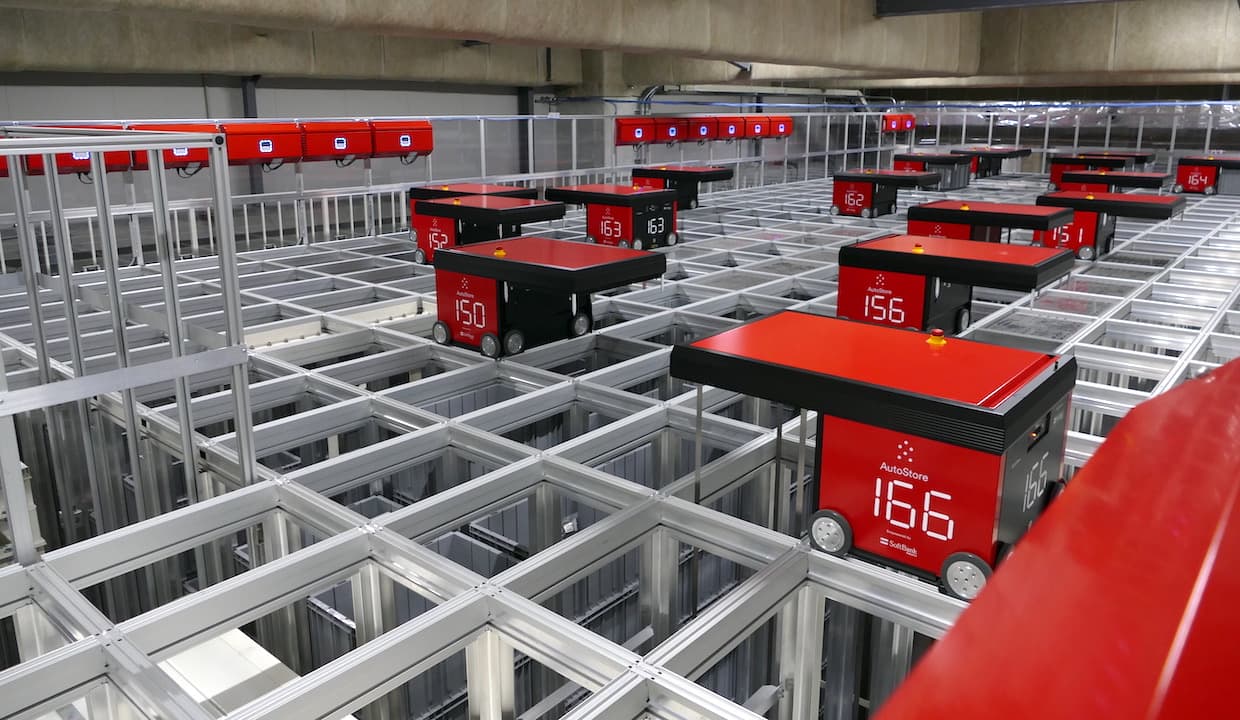
▲オートストアの自動倉庫システム
ただ、いずれも現状では人の手による作業工程を介しており、実証実験では技術的な庫内無人化に対応可能だとしても、「完全自動化倉庫」実装の本格普及は、まだ先になろう。花王が豊橋工場を入庫から出庫まで完全自動化対応としたことが報道されているが、一般的な現場では数年をかけて少しずつ環境を整えていかなければならない状況は変わらず、人との共存が前提となる。まずは紙からの脱却を経て、さらなる効率化へと一歩ずつ、人の知見やノウハウを生かしながら段階を踏んでいき、その過程で現場運用を見直し改善していくことこそが重要となるのだろう。
ともに働く人々にとって快適なシステム構築
導入した新しいオペレーションは恒久的なものではなく、運用スタイルの変化に応じた使用機器の変更など、常に運用効率を見極め、ソリューションの更新などを判断していかなければならない。庫内の5S(整理・整頓・清掃・清潔・しつけ)改善、ラック置き方法の見直しなど人間の作業環境に合わせた基本的な見直しだけでもピッキング効率を変えることができるし、そういう意味ではデータだけではなく「現場の声」を聞き取り、IT機器運用に落とし込むなど、現場と機械をつなぐ人の重要性も変わらない。システムエラー対応や、出荷頻度、季節波動の対応などからロケーションを見直してピッキングにも対応させるなど、運用を管理する人材次第で生産性も大きく変化する。
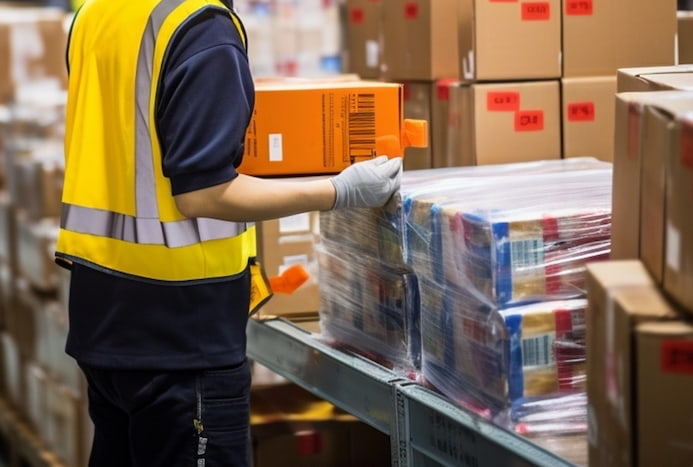
(イメージ)
誰にでも対応できる現場作りは重要だが、それは「使い捨て」を前提とした現場作りと同義ではない。多様な人材が心地よく作業できる環境でなければ、すぐにサービスの質が低下することにもつながる。効率化ツールを導入することで、スタッフにとっても快適な就労環境を提供するという観点こそが、現在のピッキング、仕分け現場には大切な要素だと言える。
仕分け・ピッキング現場の見直しは、ロケーションや在庫管理と合わせた庫内の「見える化」の入り口であり、WMS(倉庫管理システム)や拡張するマテハンとの連動など、さらなる最適化へ向けたスタートと考えるのが正しいだろう。「物流革新緊急パッケージ」においても、物流の効率化施策として即効性のある設備投資が求められている。国策として可及的速やかな対応が必要とされることから、導入促進へのさらなる後押しも期待される。人手不足という直面する危機は、サービス普及に向けたチャンス。今の物流現場を支える従業員満足度の向上においても、より良い結果を生み出せるようなソリューションの広がりが、物流現場のイメージ改革にもつながることを期待したい。