話題LOGISTICS TODAY(東京都新宿区)の赤澤裕介編集長と永田利紀・企画編集委員が登壇した、「第3回関西物流展」「第1回マテハン・物流機器開発展」の特別セミナー講演「物流ロボット導入事例、隠された『その後』を徹底追跡〜忖度なし。使えたのか、使えなかったのか〜」の現地レポート。第4回は、現場運用におけるロボットの「位置付け」について議論します。
「これ以上は無理」という場合はロボットに合わせてもらえばよい
<赤澤>
次に行きたいと思います。「うまくいかないのは荷姿がおかしいから」。これも同じようなトピックになるのかなと思いますけれども。うまくいかないのは、というのはロボットの運用ですよね。運用がなかなかうまくいかない事例が結構あるんですけれども、そういうところで本社から来た役員とか社長が「そもそも物流現場のレイアウトとか荷姿がおかしいからなんじゃないか」とかそういうもっともらしい指摘をしてしまっているということを指していると思うのですが、永田さん補足的に説明してもらっていいですか。
<永田>
物を扱う会社にはそれぞれに事情があって、私は物流上の正論を言えるのですが、ある会社にとって、それは正しくなかったというケースもありました。
例えば皆さん、誤ピック防止のためにロケーションを飛ばすというのは、どこの会社もやると思います。ある品物のSサイズ、Mサイズ、Lサイズを並べない。並べるから間違える。飛ばすんだ、と。特に返品の棚戻しで、SなのにMに入れてしまう勘違いというのは絶えないと思うのですが、それでもロケーションを飛ばすことを絶対許さない荷主企業がある。
それはなぜかというと、例えばモノを売っている会社で販売の最前線を担う店長が倉庫に来て自店舗の取扱品を選ぶ際に、棚マスにアイテム別・サイズ別に商品を並べなければ、「店長が選びにくいではないか」と。物流現場は店長がやりいいように合わせるんだよという会社があって、それはその会社の正義。
似たような事例として無人の搬送機やハンドアームが想定通りに稼働しないのは荷姿がおかしいからであるというマテハンメーカー。「表示している耐荷重とか荷上げできる重さいっぱいに使うには、こういう形のものは無理です」というポイントがあるんですけれども、その荷主企業にとって現状の荷姿というのは、長年かけて工夫して作り上げたものなわけですね。そうするとこういう言葉は通じない。
今から自動化でどんどん現場に機械が入ってくると、会社の創業理念まで干渉するような問題になってきて、途中で頓挫することも多くなってくると思います。こういう荷姿やロケーションの取り方の問題において、出来上がったところだけを見て導入を決定するのはちょっと危険かな、と。例えば自動化して誤出荷がゼロになっている企業は、誤配送がゼロになっているだけで、誤ピックがゼロになってるいるかどうかの検証はあまりしません。
誤配送ゼロと誤ピックゼロは違うんだと、今一度皆様にご確認いただきたいと思います。知らぬ間にWMS(倉庫管理システム)病になっていて、多少雑であっても、派遣の若い男の子が体力に物を言わして、このピッキングリスト10枚、1時間で全部取ってくれ、と。それでピコピコ、スキャン。そこでなんとか引っかかって誤配送にはなっていないんですけど、誤ピックにはなっている。自社物流ならば「うちの会社の物流は自社製品のピッキングすらちゃんとできていないのか」と経営層から嘆きが漏れるいう会社はすごく多いんですね。
なので、誤ピックをしないところに本当は力を入れていかなければならないのに、誤ピックしても大丈夫なところに非常に注力している。人間は誤ピックすると決まっているのだから、誤ピックしてもいいように機械にさせる。あるいは保険をかけるという意味では正しいのですが、本当にそれでいいのか、と一度皆さんに考えていただきたいなと思います。
あまりにもちょっと寂しい。誤ピックしないやり方を諦めなきゃいけないほど、努力して工夫してきたのか。意外と止まりますよ。お金かけなくても頭にねじりはちまきで、現場のトップが本気でやるとかなり止まります。自動化の前に考えていただきたい。その上で自動化とかWMSという素晴らしい機械を入れていくと、ほぼ完璧に止まる。仕上げで使っていただくのがいいのではないかと思います。荷姿についても同じ。自動化するにあたって、この荷姿をここまで機械に合わせたけど、これ以上は無理という場合は機械に合わせてもらいなさい、と。この思考は忘れないでいただきたいと思います。
最大の問題は、「結果だけで決める」経営陣に「ノー」と言えない現場環境だ
<赤澤>
ありがとうございます。今のって運用の話じゃないですか。さきほど紹介したアンケート結果を思い出していただきたいんですけど、発注間際に断念したって話があったじゃないですか。実はロボットの導入に対して成功か失敗かを語るときに、導入した後にうまくいった・うまくいかなかったの話も、もちろんその主流の話としてあるんですけれども、実は表に出てこない情報として、導入をチャレンジしたんだけど結果的に導入に至らなかったという事例をものすごく聞くんですよ。
そこって無視していい話なのかな、どうなんだろうと思うんですね。ひょっとしたらそこでのつまずきが、導入後に影響するところがあるんじゃないかなと考えまして。例えば、導入にかかる時間もものすごく今長くなっているらしいんですね。AGV(無人搬送車)で6か月ぐらい。AMR(自律走行搬送ロボット)だと13か月待ちみたいな、そんな話になっているらしいですね。導入のリードタイムだけじゃなくて、導入前のプロセスでいろんな落とし穴がありそうなんですけれども、永田さんどう思いますか。
<永田>
経営陣が結果だけみて決めちゃう。自分の会社の物流のこと、現場のことがよくわかっていないので、でき上がった餅を食べるところから物語が始まっていて。餅を絵に書くところから計画しないといけないんですけど、もう美味しい美味しいと食べてるところから会議が始まると。社長そんな餅食べれないですよ、と。まず絵に描いたようなこんな餅ないし、というようなところで。ノーを言えない環境が一番問題なんだと思いますね。今おっしゃった、6か月とか13か月っていう期間も、掛ける2ぐらいですね。
<赤澤>
そうですか。それはちょっと、くじけちゃいますね。導入に至るまでリードタイムが、ものすごく長期化、長時間化しているんですよね。私が取材しながら感じた理由としては、大体この2つぐらいあるかなと思っております。一つは、やっぱりロボット本体に目がいきすぎて、実際に物流センターや倉庫の中で運用する上では、一部分なわけじゃないですか。前後の連携がなかなかおろそかになっていて、そこをちゃんとしないと、最終的にはオペレーションとしてつながらないわけですけれども、ものすごく時間が取られる。特にWMSのカスタマイズ、ここに時間も費用も想定外のものが取られてしまって、断念せざるを得なかったみたいな話がすごくあります。
実はそのあたりって、WMSにもいろんなパターンがあってですね。サブスク型も最近増えてきましたし、個建てでカウントするものとか、あるいはしっかりとオンプレミス型で導入していくもの、自社開発のもの、いろんなものがあると思いますけれども、そのあたりロボットとの連携を重視しているWMS選びも実は重要だったりします、というところが一つ。もう一つは、実は物流側からは改善やアプローチができるものじゃないかもしれないんですけれども、今世界的にやっぱり半導体不足があります。これがですね、実は日本の物流現場においてロボット導入のかなり大きな障害になっていると感じました。どういうことかっていうとですね、ロボットって今は別に物流だけじゃなくていろんな業界がロボットの導入を考えております。しかも日本だけじゃなくて、中国もアメリカもヨーロッパもみんな考えてるんですよ。
そういう中で日本の物流現場から出てくるロボット導入ニーズが、ロボットメーカーにとってどれぐらいの需要・シェアがあるのかと考えたら、実はそんなに大きなシェアではないのが一つなんですね。さらにさかのぼって、さらに上流にいくと、ロボットの主要パーツってAI(人工知能)とかそういうものよりも、実は今一番足りないのが、モーターらしいです。モーターが手に入らない。大口の製造業は、そのモーターを大口発注してあらかじめ数を確保してるケースも多いんですけれども、そのモーター屋さんから見ると、物流ロボットメーカーから発注されるモーターの発注数って、1回に5個とか、それくらいらしいんですよ。それは買い負けますよね。
それが日本の中で今こんなに気持ち的にはロボット導入に向けて盛り上がっているのに、先ほど13か月とか、倍で考えた方がいいんじゃないか、と永田からの指摘ありましたけれど、背景にはそんなところもあります。何かちょっと悔しいですよね。日本の物流って、日本の産業競争力下支えする、今や主力産業なんですけれども、実は購買力の弱さがロボット導入の足かせになってしまっている面もあるということです。
第5回は、ロボットへの適正な「期待値」のあり方を探ります。
■物流ロボット特集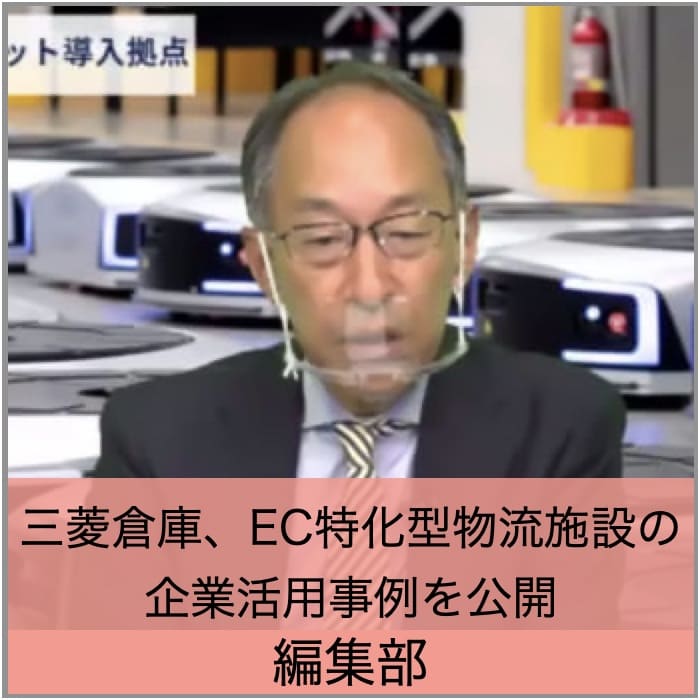

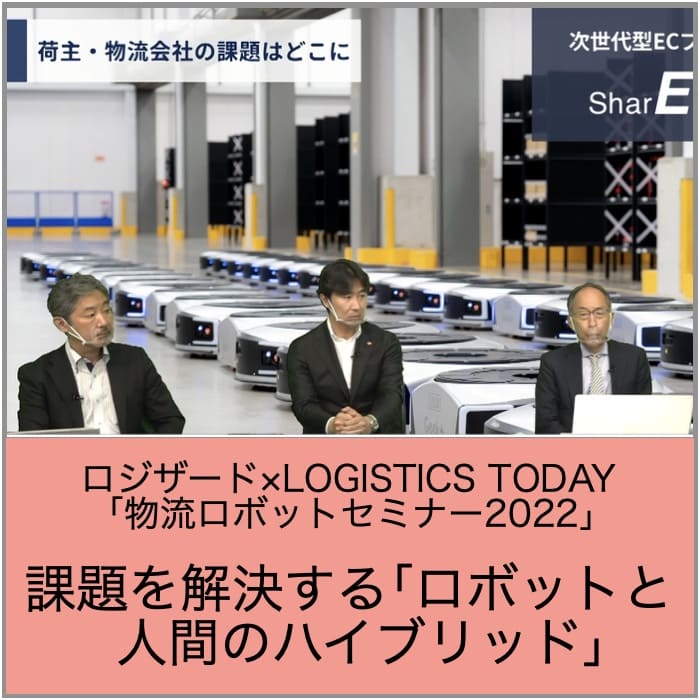


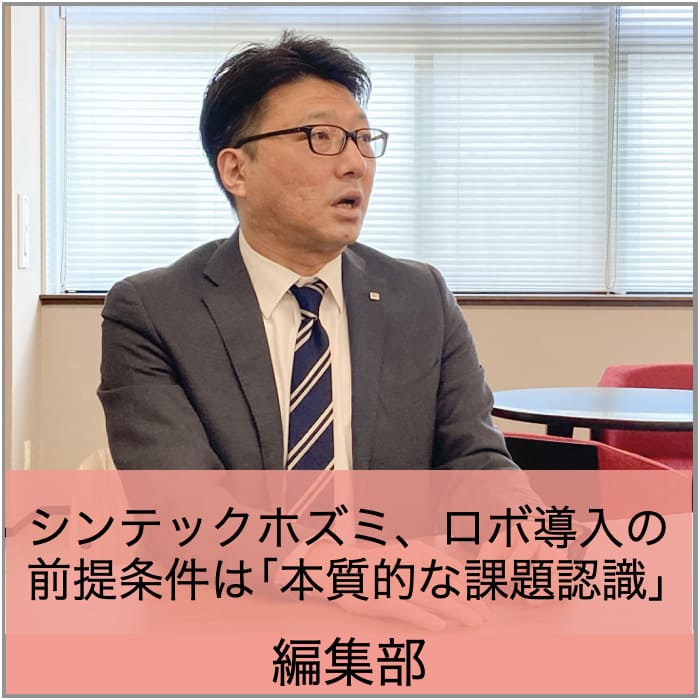

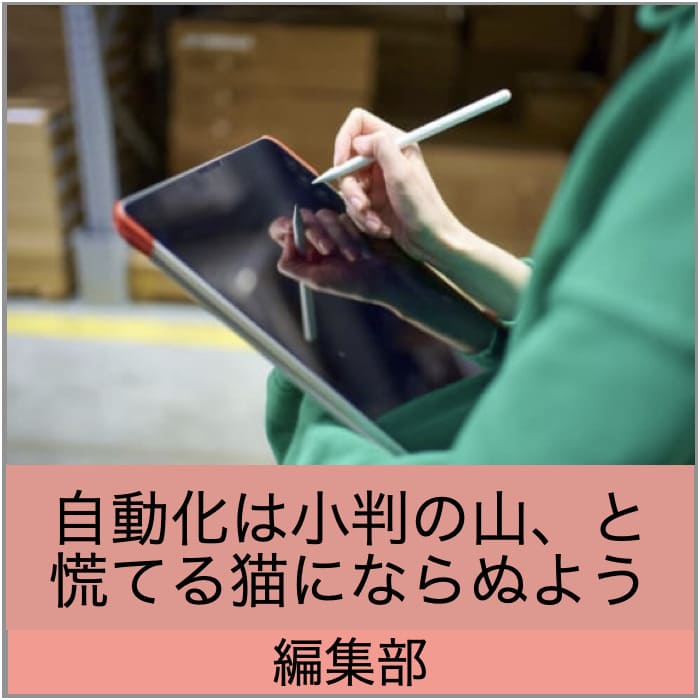

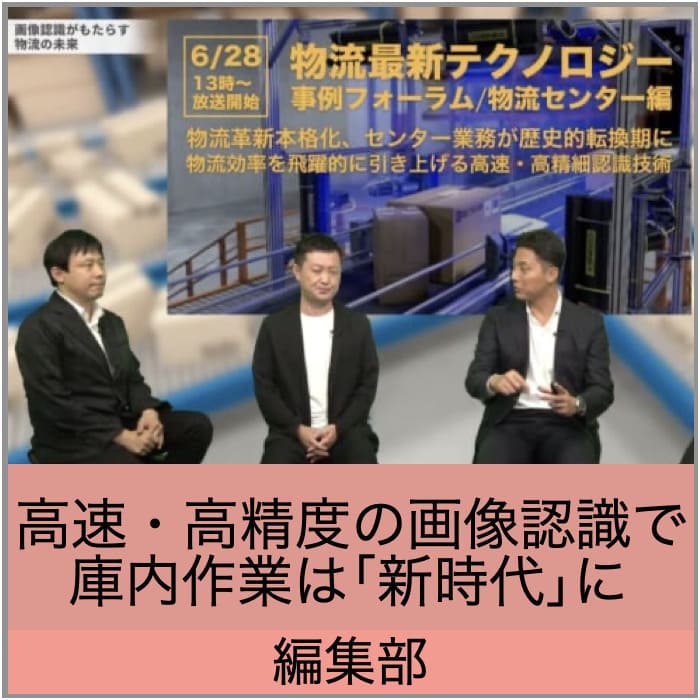
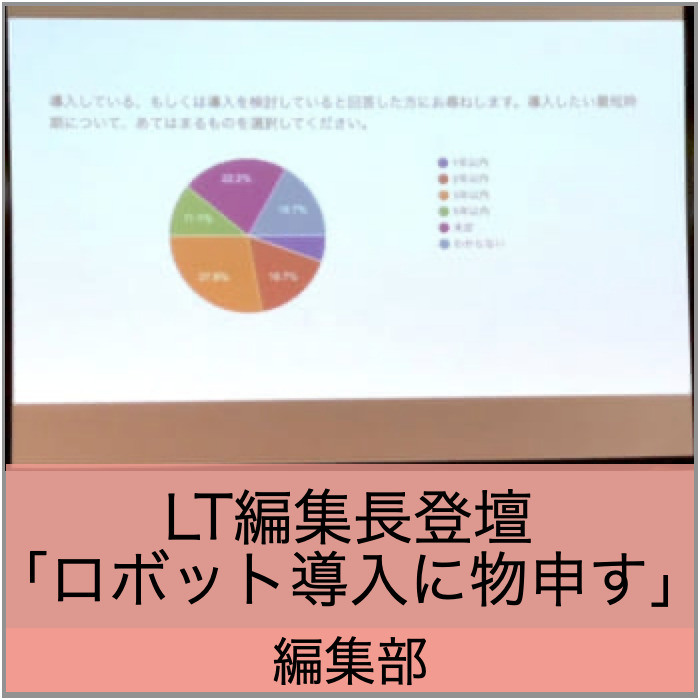

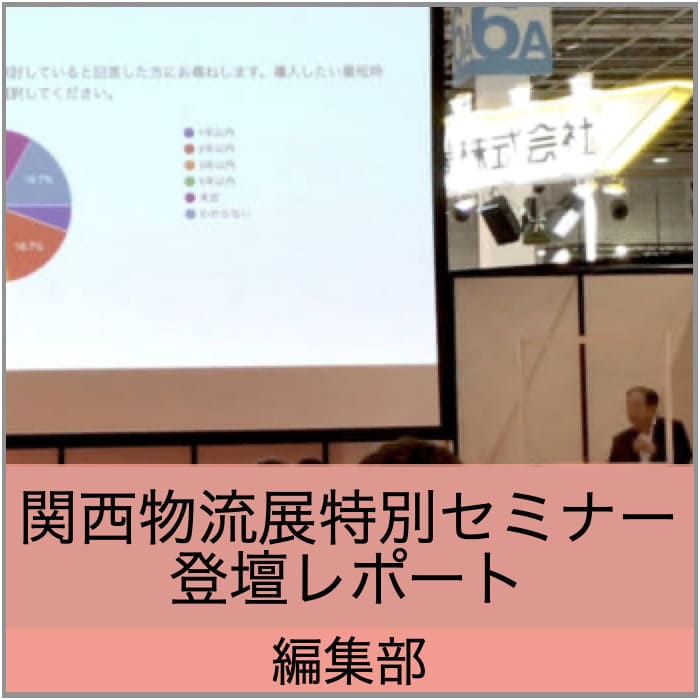

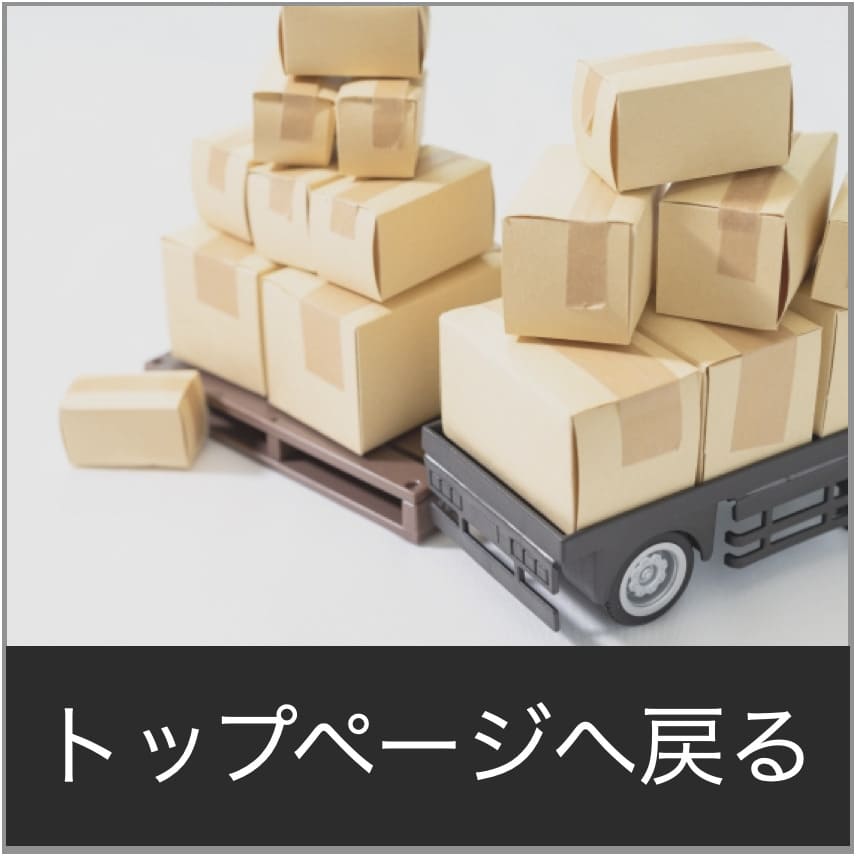