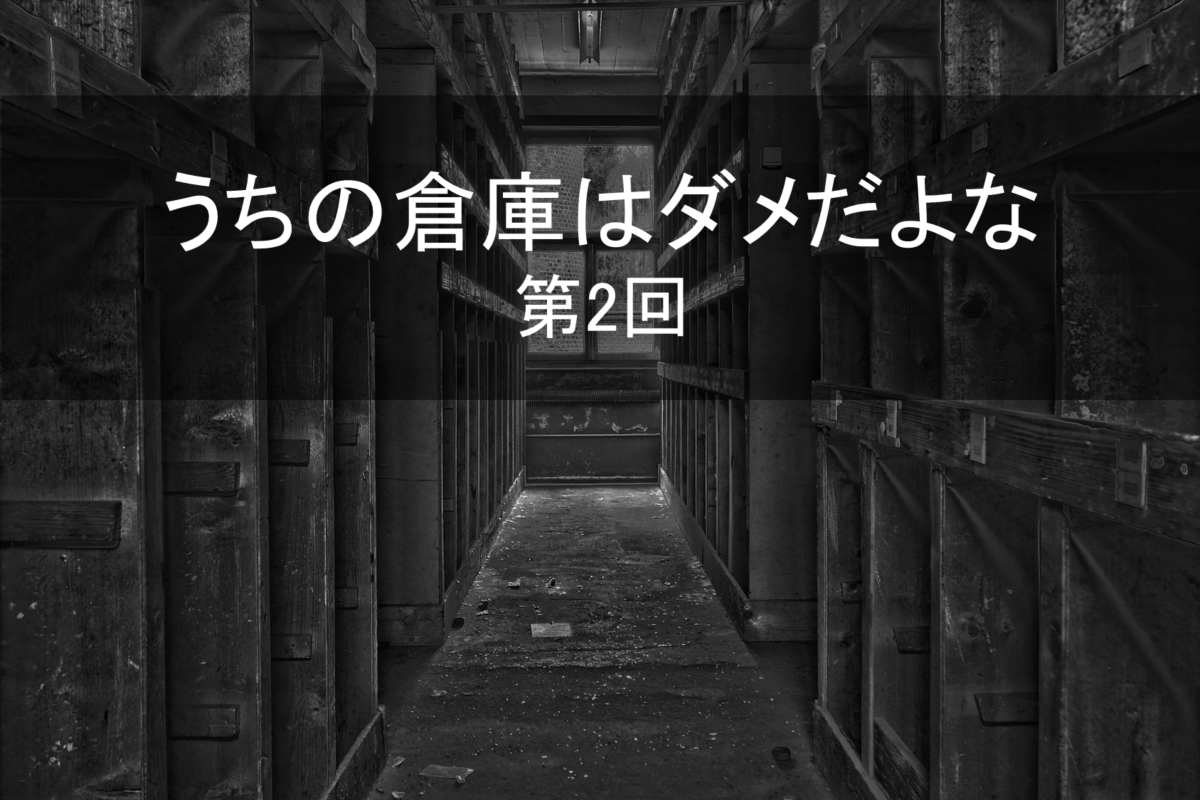
話題企画編集委員・永田利紀氏のコラム連載「うちの倉庫はダメだよな」の第2回を掲載します。ある物流部門の現場責任者「A課長」の独り言から展開していきます。
https://www.logi-today.com/417822
■営業部からのクレーム
また営業からクレームだ。P社への誤出荷らしい。今月に入って二回目だ。一回目は入数不足だった。今回のは品番違い。
アナログ作業でのバラ出荷だから完全に防げないのが実情なのだが、それは禁句だ。開き直りとしか思われないだろうし、ミス時の言い訳は火に油を注ぐことにしかならない。
「営業がせっかくコツコツと苦労して受注し、やっと納品したと思ったら出荷ミスで今までの努力が帳消しになってしまう。それどころかマイナスに落ち込んで、何度か続くと発注が来なくなってしまう」という事態にまで達したら、物流部はどう責任を取るつもりなのか?という闇からの声が耳に居残ったまま何年も過ぎた。
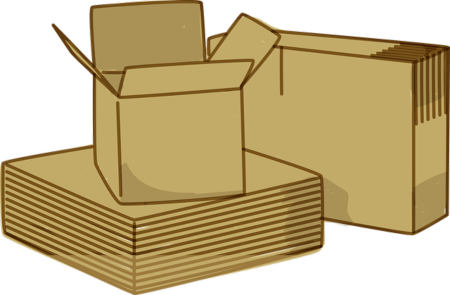
(イメージ画像)
ひと昔前まではこんなミスはほぼゼロだった。入数不足などありえないし、品番違いのまま納品されることなどなかった。なぜなら小さな部品や部材は入荷も出荷も「箱」単位だったからだ。自社製品の箱には、全てJANコードと品番が印字されたシールが貼付されている。入荷時にスキャンして入庫確認・入荷計上の後に、入荷指示にあるロケへ棚振りする。
その際にもロケシールのバーコードと再度製品箱のJANをそれぞれスキャンして、手許の端末画面で正常処理の「◯」印が表示されれば、無事に完了となる。だから誤入荷による在庫差異や、その後の誤ピッキングしていないのに誤出荷になってしまうといった類のミスはあり得なかった。そもそもピッキング時にも入荷と同じ理屈の作業手順でミス防止し、さらに梱包時に納品明細書のバーコードと梱包品のすり合わせをスキャンして再確認するのだ。
これらの手順を守っていれば、誤出荷や在庫差異はほぼ防げる。たまに発生するのはあきらかな人為的ミス…ルール無視やOJT不足だと決まっていた。前々任の物流部長が異動する直前までは「物流部門は仕事が簡単で余裕がある」と社内で揶揄されたりもしていたが、ミスなしで在庫もあっていたので評価自体は悪くなかった。

(イメージ画像)
10数年前から始まった顧客サービスの徹底的な見直しと商材入替による営業力強化の掛け声のもと、さまざまな試みが行われたが、その中のひとつが製品の「バラ販売」だった。世紀が変わったこの20年来、電材業界ではEC販売の台頭によって販売単位が小さくなる傾向が顕著だ。
しかし従来の箱単位・梱包単位を前提としたまま製造現場や輸入先の海外メーカーは倉庫に納品してくる。箱や梱包の中にある製品単体には、倉庫内作業に必要な情報が付されていない。
たとえば結線用の小さな部品にバーコードの貼付は不可能だし、それを1個とか5個単位で小袋に詰めてシール貼付すれば、その分製造コストが上がり、OEMの仕入品なら割高になる。現在の国内市場環境でコスト転嫁型の製品値上げは論外だ。
その結果として、仕入の「できない」と営業の「やろう」を両方聞き入れて汗をかくのは物流部となっている。箱の外にあるJANは入数100の1箱に付されたものではなく、中身のバラ1個を示すコードに設定変更された。だから13というバラピックが12や14になっていたり、1というピッキングで100、つまり1箱が出荷されてしまったりが起こってしまう。とある製品のサイズ違いφ8とφ10とφ12のバラピックで3品番のピッキング個数が同一だったり違っていたり、そのパターンが一枚のピッキングリスト内に15行あったりすると、何度かに一度は行テレコ・ピックや単純な数取り間違いするが、梱包時に引っかからなければそのまま「行ってしまう」のだ。
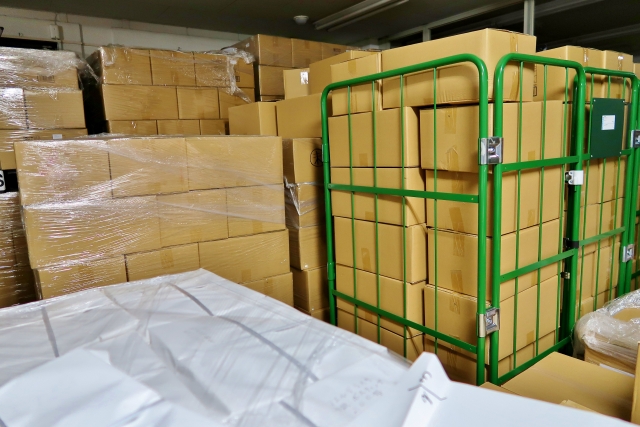
(イメージ画像)
目検による品番確認と検数。気のゆるみや怠慢などなくても、ミスの可能性は常在する。目で見ながら手に取って声に出して数えても間違いはゼロにはできない。重ねて段差感触を探ったり、並べて凝視、もしくはノギスでしか測定できないミリ単位の差など、人間の視覚や触覚で完全に判別することなど無理に決まっている。平均時給950円のパート従業員に神業のような職人芸や熟練を求めることは論外だし、そもそも現場作業者にルール順守と時間効率以外を求めること自体が運営エラーなのは管理業務の基本だ。という倉庫現場での基本的なルールと本音は部内でしか認められない。
結果的には何もかわらないまま毎月数件のミスが発生する。「今の庫内作業条件と環境ではミスゼロの継続は難しい」、という先回りした発言は、その理由と真意の詳細な説明の機会を待たず怠慢や努力放棄とみなされてしまう。
「がんばります」「努力します」以前に「前提条件を変える必要がある」「アナログでの業務フローには限界がある」などを要求することは、怠慢者の言い訳と評価されかねないだろう。他社のことはわからないが、わが社では精神論ありきの仕事心得がまかりとおっている。「他部門だって主張や言い訳したいことを呑み込んで、身を削りながらやっている」はあらゆるミス発生時の釈明や説明を引き受ける下の句として万能なのだ。
前任の物流部長は準大手の物流会社からの中途入社だったが、前提条件の変更や現状での限界を役員会で強く訴えた結果、その二か月後には子会社の管理部門へ出向となってしまった。「管理業務改革PJの責任者として、求められての異動」と聞いているが、その後のことは知りようもない。
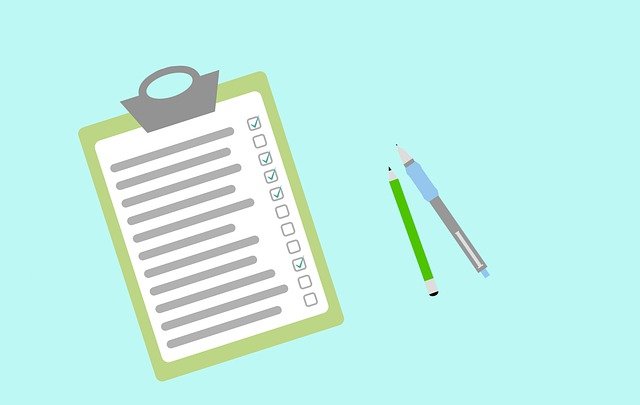
(イメージ画像)
個客注文への柔軟な対応に異存はない。しかし、我々のような製造会社が一定の発注単位を基本として顧客に「お願いする」ことは怠慢や自己本位に過ぎることだとは思えない。たとえば今回誤出荷したP社にしても、入数不足だった品番の製品は月あたり1.7~1.9箱という範囲内で発注がかかる。ならばなぜ月に2箱の納品交渉を営業はしないのだろう。過去に何度も取引先別の納品パターン・データの一覧を提出しているが、一向に適用される気配はない。おそらくだが、顧客はそんなデータの存在すら知らないのだろう。
個客の便宜を図ることが小分け受注導入の目的だったはずだ。しかし結果的には倉庫の作業条件が悪化して、何度も誤出荷してしまっている。「顧客本位」への視点と注力が一面的すぎると思うのだが、まさかそれを面と向かって営業の役職者に指摘する気にはなれないし、それ以前に物流部の総意としてすらまとまりそうもない。庫内作業の努力だけでは完全な解決は難しいことなど自明だが、部長は営業に申し入れる気は全くないようだ。「できることはまだあるはずだ」という毎回同じ締めの言葉で月次会議は終わる。
―第3回(2月15日公開予定)に続く
コハイのあした(連載9回)
https://www.logi-today.com/361316
BCMは地域の方舟(連載3回)
https://www.logi-today.com/369319
駅からのみち(連載2回)
https://www.logi-today.com/373960
日本製の物流プラットフォーム(連載10回)
https://www.logi-today.com/376649
もしも自動運転が(連載5回)
https://www.logi-today.com/381562
あなたは買えません(連載5回)
https://www.logi-today.com/384920
物流人になる理由 (連載6回)
https://www.logi-today.com/400511
保管料商売はやめました(連載8回)
https://www.logi-today.com/408179
■時事コラム
“腕におぼえあり”ならば物流業界へ
https://www.logi-today.com/356711
-提言-国のトラック標準運賃案、書式統一に踏み込め
https://www.logi-today.com/374276
物流業界に衝撃、一石”多鳥”のタクシー配送
https://www.logi-today.com/376129
好調決算支える「運賃値上げ」が意味すること
https://www.logi-today.com/377837
ヤマトのDM便委託は「伏線回収」の始まりか
https://www.logi-today.com/401241
コロナ発生時の初動、天災が人災と化すことを危惧
https://www.logi-today.com/406463
越境ECは死語になるか、菜鳥網絡日本参入の意味
https://www.logi-today.com/407525
タクシー配送、まずは規制緩和へのロードマップを
https://www.logi-today.com/409146
■取材レポート
業界の“風雲児”MKタクシーに聞く「タク配」の可能性
https://www.logi-today.com/380181
その仕事、港湾でもできますよ -兵機海運取材レポート-(連載3回)
https://www.logi-today.com/386662